Exactly How Specialist Packaging Maker Repair Work Solutions Lessen Downtime and Boost Efficiency
Specialist product packaging equipment fixing solutions are crucial in lessening downtime and improving efficiency with specialized diagnostics and prompt treatments. The ramifications of such solutions extend past instant repairs-- unboxing the wider effect on functional efficiency reveals crucial understandings into long-term productivity methods.

Significance of Timely Fixes
Prompt repairs of packaging makers are vital for maintaining functional efficiency in any manufacturing atmosphere. When machinery malfunctions or breaks down, it can lead to significant disturbances in manufacturing lines, causing boosted downtime and shed profits. The longer a packaging device remains out of order, the higher the influence on general productivity, possibly triggering delays in fulfilling orders and reducing customer fulfillment.
In addition to the instant financial effects, postponed repair services can cause a lot more comprehensive damage to the machinery. Elements that are not attended to promptly can wear away better, requiring more pricey repair work or complete replacements, which can have been stayed clear of through prompt treatment. Normal maintenance and punctual repair services can enhance the life-span of packaging devices, guaranteeing that they run at ideal performance levels.
Spending in professional packaging device repair solutions is necessary for mitigating these threats. An aggressive method to repair work not only keeps manufacturing timetables yet additionally promotes a society of reliability within the company. By focusing on timely repair services, organizations can maintain their one-upmanship, enhance source allocation, and eventually enhance their lower line with improved functional effectiveness.
Knowledge in Diagnostics
When it comes to maintaining the efficiency of packaging machines, proficiency in diagnostics plays an essential duty in identifying problems prior to they escalate into major failures. Experienced service technicians make use of innovative analysis devices and techniques to execute detailed analyses of machine performance. This proactive method enables them to pinpoint the origin of malfunctions, whether they come from mechanical wear, electric faults, or software inconsistencies.
Efficient diagnostics not only assist in speedy recognition of troubles but likewise boost the overall dependability of packaging procedures. By carrying out extensive examinations, service technicians can evaluate the health of essential elements, ensuring that even small irregularities are dealt with without delay. This focus to detail minimizes the risk of unexpected malfunctions, which can bring about expensive downtime.
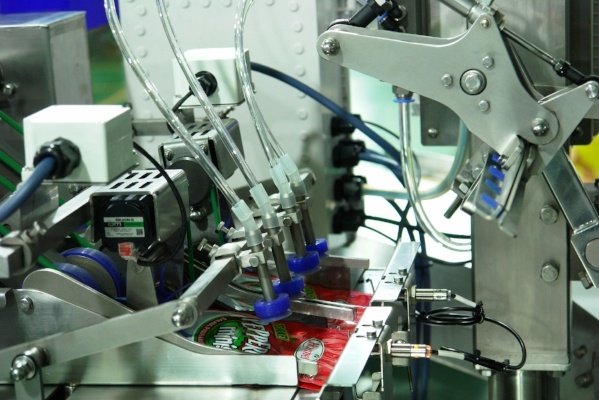
Preventive Upkeep Advantages
Preventive upkeep enhances specialist diagnostics by proactively dealing with potential issues prior to they materialize into serious issues. By implementing a structured preventive upkeep program, companies can considerably minimize the risk of unforeseen equipment failings, therefore minimizing costly downtime. Routine examinations, cleansing, and parts replacement aid guarantee that packaging equipment runs at ideal efficiency.
Additionally, preventive upkeep contributes to enhanced security conditions within the workplace. By recognizing and fixing possible threats prior to they escalate, organizations produce a much safer setting for why not look here their employees. This proactive technique not just safeguards workers but likewise promotes a culture of Learn More obligation and caution.
Lastly, regular preventative maintenance can enhance product high quality. Properly maintained devices runs more regularly, reducing the possibility of flaws and making certain that product packaging fulfills rigorous industry requirements. In recap, preventative upkeep is a crucial method for optimizing efficiency and making sure operational quality.
Customized Solution Solutions
Recognizing the special demands of each organization, personalized solution remedies for product packaging machine repair work deal customized techniques that enhance operational effectiveness. These services are made to attend to specific difficulties dealt with by various markets, guaranteeing that equipment downtime is minimized and productivity is made best use of.
Expert fixing solutions start with a detailed analysis of a company's packaging operations. By understanding the particular machinery included and the demands of the production environment, service technicians can create an individualized upkeep and fixing strategy. packaging machine repair service. This may include specialized training for in-house team, the application of predictive maintenance innovations, or the provision of dedicated assistance during peak manufacturing times
Moreover, tailored services can include adaptable service arrangements that line up with a firm's functional timetable, enabling repairs to be executed throughout off-peak hours. By prioritizing the one-of-a-kind demands of each business, these custom solutions guarantee that repair services are not just efficient yet additionally perfectly incorporate into existing operations.
Ultimately, the concentrate on customization makes it possible for companies to maximize their product packaging procedures, bring about improved reliability and efficiency of equipment, which is critical for maintaining competitive benefit in today's busy market.
Influence On General Performance
Customized service options not only address certain repair needs however additionally play a significant function in enhancing total operational effectiveness. By giving targeted treatments, expert product packaging maker fixing solutions directly reduce the frequency and period of tools failings. This aggressive technique ensures that manufacturing lines stay operational, lessening disturbances that can bring about expensive downtime.
Additionally, reliable repair service services contribute to smoother operations, as well-kept equipment runs at optimum efficiency degrees. When makers function appropriately, the high quality of packaged items improves, bring about less defects and less rework. This enhancement not just enhances performance yet likewise strengthens customer complete satisfaction.
Furthermore, normal upkeep and quick reaction times from repair service experts promote a society of reliability within the company. Workers can focus on their primary tasks instead read more than fretting about possible equipment failures. As a result, the total throughput of the production process increases, permitting business to satisfy demand much more efficiently.
Ultimately, the critical financial investment in specialist repair work services converts to boosted effectiveness throughout all operational facets, making certain that organizations can adapt and prosper in a competitive market. This synergy in between maintenance and performance is important for long-term success.
Verdict
Finally, professional packaging equipment repair work solutions play an important function in minimizing downtime and boosting performance within manufacturing environments. Timely repair work, expert diagnostics, and precautionary maintenance add to the integrity of devices, while personalized solution remedies attend to specific functional needs. The collective impact of these services results in enhanced general performance, making it possible for businesses to keep manufacturing timetables, promote product high quality, and properly meet market demands - packaging machine repair service. Investing in such services ultimately drives sustained operational success.
Comments on “Skilled packaging machine repair service for ensuring operational success.”